The Low Pressure Casting Process: Revolutionizing Manufacturing
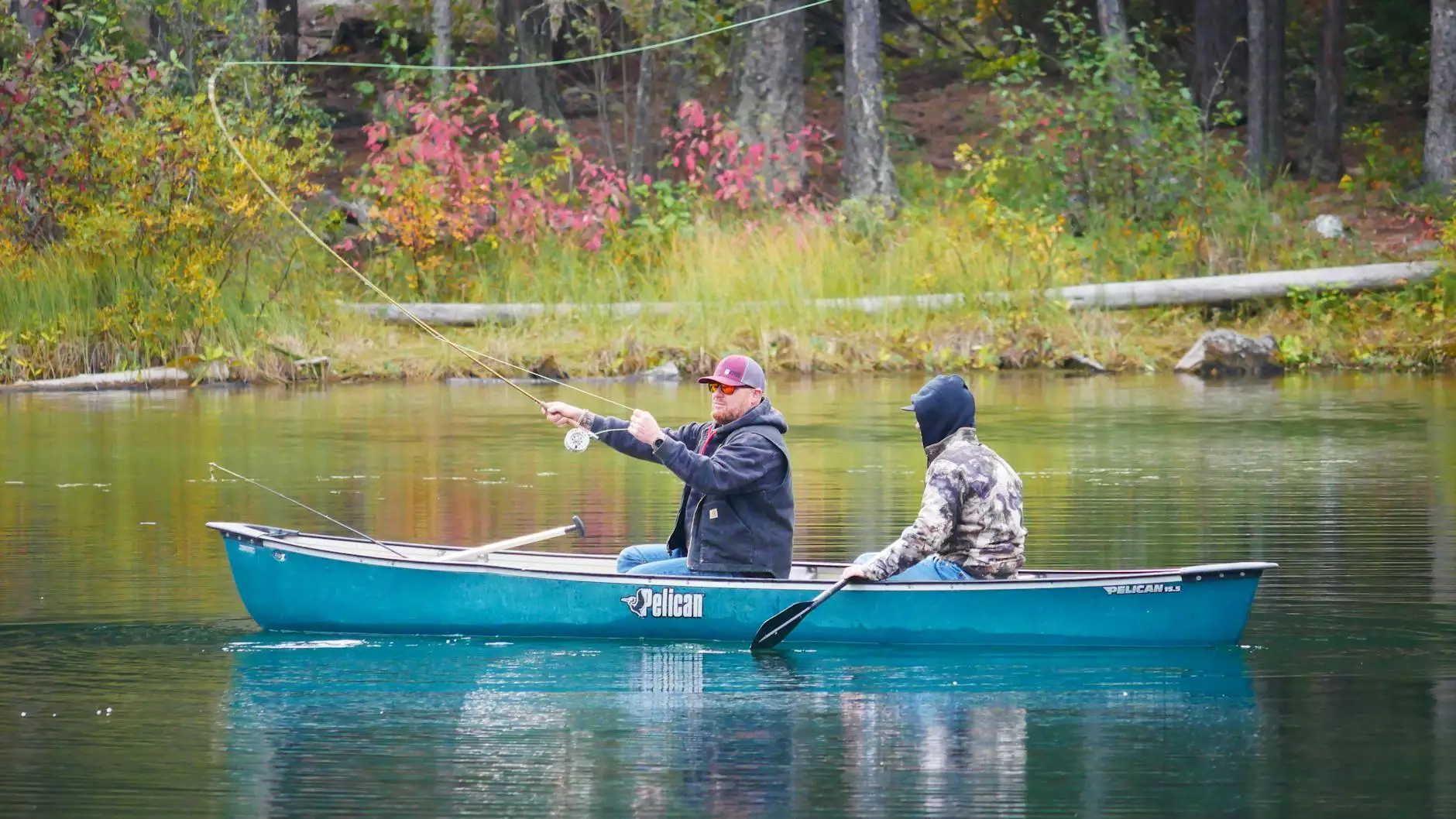
The low pressure casting process is a game changer in the manufacturing sector, particularly for businesses involved in art supplies, product design, and advanced 3D printing solutions. As market demands evolve, the need for precise, cost-effective, and high-quality manufacturing methods becomes even more critical. This article delves deep into the intricacies of the low pressure casting process and its transformative effects on various industries, showcasing its benefits and applications.
What is Low Pressure Casting?
Low pressure casting (LPC) is a technique used in the manufacturing of metal parts where metal is poured into a mold under low pressure conditions. This method allows for greater control over the casting process, producing components with impeccable accuracy and minimal defects.
- Energy Efficiency: Utilizes less energy compared to other casting methods.
- Precision: Achieves higher dimensional accuracy.
- Quality: Reduces occurrences of porosity and inclusion defects, resulting in superior products.
- Cost-Effective: Low tooling costs with high production rates.
The Advantages of Low Pressure Casting
With numerous casting techniques available, the low pressure casting process stands out due to its specific advantages, making it an attractive option for businesses in today’s competitive landscape.
1. Enhanced Product Quality
The low pressure casting process significantly minimizes the defects traditionally associated with higher pressure casting methods. The gentle filling of the mold reduces turbulence, which leads to a more uniform distribution of the molten material. This results in a denser final product, which is essential for applications needing high strength and durability.
2. Reduced Material Waste
Another notable benefit is the reduction of material waste throughout the process. Because the LPC method utilizes a controlled environment, there is less excess material produced. This not only conserves resources but also contributes to a more sustainable manufacturing practice.
3. Versatility in Design
The low pressure casting process allows for intricate designs that may be challenging with traditional methods. Businesses involved in product design can leverage this flexibility to create complex geometries that meet the ever-evolving demands of consumers.
Application in Art Supplies
For companies focusing on art supplies, the ability to produce custom molds uniquely positions them in the market. Low pressure casting empowers artists and designers to explore new mediums and materials, allowing for limitless creativity.
Application in 3D Printing
Moreover, as the world of 3D printing continues to expand, the low pressure casting process can complement additive manufacturing techniques by providing robust and detailed parts that interact seamlessly with 3D-printed components. This integration enhances product offerings and builds a sustainable ecosystem of manufacturing processes.
Understanding the Low Pressure Casting Process
The low pressure casting process involves several critical steps that are essential for successful outcomes. Let us break down the process:
Step 1: Mold Preparation
Proper mold preparation is crucial to ensure that the parts produced are free of defects. Molds can be made from various materials, including steel, aluminum, or even non-metal substances, depending on the intended application. Once prepared, they are placed in the casting machine.
Step 2: Heating the Metal
The metal, typically aluminum or zinc, is heated to its melting point in a furnace. This molten metal must maintain a constant temperature to ensure it flows correctly into the mold.
Step 3: Applying Low Pressure
Unlike conventional casting methods, where gravity is the driving force, the low pressure casting process implies that a controlled air pressure is applied. This pressure gently forces the molten metal into the mold, filling it uniformly and quickly.
Step 4: Cooling and Solidification
Once the mold is filled, the molten metal cools and solidifies. This cooling process is carefully controlled to prevent any thermal shocks or stresses that could lead to defects.
Step 5: Demolding and Finishing
After the metal has completely solidified, the mold is opened, and the casting is removed. Further finishing processes, such as machining or surface treatments, can be applied to achieve the desired properties.
The Future of Low Pressure Casting in Business
As we look towards the future, the low pressure casting process is poised to play an integral role in the evolution of manufacturing. With increasing demands for customization, sustainability, and efficiency, this method offers a viable solution to meet such challenges.
Embracing Industry 4.0
With the rise of Industry 4.0, manufacturers are integrating smart technologies into their systems. The low pressure casting process can benefit significantly from automation, IoT, and data analytics, allowing businesses to maximize efficiency and minimize downtime.
Impact on Sustainability
As global awareness of sustainability increases, businesses recognize the necessity to adopt eco-friendly practices. Low pressure casting’s potential to reduce waste and energy consumption aligns perfectly with sustainable manufacturing principles, enabling companies to meet regulatory requirements and consumer expectations.
Conclusion: Transforming Business with Low Pressure Casting
In conclusion, the low pressure casting process offers unparalleled advantages that can lead to substantial improvements in the quality, efficiency, and sustainability of manufacturing operations. Companies like Arti90, which focus on art supplies, product design, and 3D printing, can leverage this technology to deliver innovative solutions that stand out in the marketplace.
As industries evolve, investing in advanced manufacturing techniques like low pressure casting will not only enhance product offerings but also establish a competitive edge. Embrace the low pressure casting process and unlock the potential for growth and innovation in your business today!